- Home
- Sponsors
- Forums
- Members ˅
- Resources ˅
- Files
- FAQ ˅
- Jobs
-
Webinars ˅
- Upcoming Food Safety Fridays
- Recorded Food Safety Fridays
- Upcoming Hot Topics from Sponsors
- Recorded Hot Topics from Sponsors
- Food Safety Live 2013
- Food Safety Live 2014
- Food Safety Live 2015
- Food Safety Live 2016
- Food Safety Live 2017
- Food Safety Live 2018
- Food Safety Live 2019
- Food Safety Live 2020
- Food Safety Live 2021
- Training ˅
- Links
- Store ˅
- More
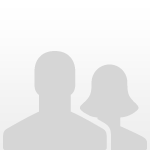
Non-conformance SQF audit for not carrying out environmental swabbing
Started by Aartisharma98, Dec 07 2023 03:37 PM
8 replies to this topic
#1
Posted 07 December 2023 - 03:37 PM
Hi everyone,
I have a question in regards to sqf audit corrective action.
environmental swabbing not done for months of june and september. what should be my course of action?
is it swabbing the surfaces for the months june and september and showing the results to the auditor?
Kind Regards,
#2
Posted 07 December 2023 - 04:33 PM
Dear Aartisharma98,
What is the frequency of the environmental testing?
If it is quarterly and you did not do it in June and September and next testing planned is January, you should as correction do it now.
If the frequency is monthly and you did the tests in October, November and December a correction is not possible and you should focus on the corrective actions.
Corrective actions depends on your root cause.
What is the root cause of not performing the environmental testing?
E.G.: Was the resonsible person on holiday, the corrective action can be to apoint a deputy and show nomination and training records of this deputy.
Kind Regards,
Madam A. D-tor
Madam A. D-tor
Thanked by 1 Member:
|
|
#3
Posted 07 December 2023 - 04:34 PM
Need more context
schedule frequency etc
Please stop referring to me as Sir/sirs
Thanked by 1 Member:
|
|
#4
Posted 07 December 2023 - 04:34 PM
Greetings!
I'm going to jump in here. This is what I think the auditor wants to know...WHY weren't the swabs done in June and September?
Who was/is responsible for doing this?
Why wasn't there a back-up plan to make sure that this happened?
What are you doing to ensure that this does not happen again?
Who will monitor this?
- SQFconsultant likes this
-Setanta
Thanked by 1 Member:
|
|
#5
Posted 07 December 2023 - 04:43 PM
Need more context
schedule frequency etc
Dear Aartisharma98,
What is the frequency of the environmental testing?
If it is quarterly and you did not do it in June and September and next testing planned is January, you should as correction do it now.
If the frequency is monthly and you did the tests in October, November and December a correction is not possible and you should focus on the corrective actions.
Corrective actions depends on your root cause.
What is the root cause of not performing the environmental testing?
E.G.: Was the resonsible person on holiday, the corrective action can be to apoint a deputy and show nomination and training records of this deputy.
frequency of the environmental testing IS MONTHLY. ACC,E.Coli,Coliform is done every month and salmonella/listeria quarterly. missing months were ACC,E.Coli,Coliform swabs. correction : its july and october which was missed. No swabbing was done for the month of october and july samples arrived to the lab in warm temprature (no ice packs). There's only one designate no one else. i'm the new guy i just joined a month ago
#6
Posted 07 December 2023 - 04:48 PM
Greetings!
I'm going to jump in here. This is what I think the auditor wants to know...WHY weren't the swabs done in June and September?
Who was/is responsible for doing this?
Why wasn't there a back-up plan to make sure that this happened?
What are you doing to ensure that this does not happen again?
Who will monitor this?
its july and october which was missed. No swabbing was done for the month of october and july samples arrived to the lab in warm temprature (no ice packs) also end of july.
There's only one designate no one else. i'm the new guy i just joined a month ago
#7
Posted 07 December 2023 - 05:09 PM
OK, new person on the job. I'm sorry, it's going to be tough.
You will need to make contingency plans. You will need to document all the changes you will make to your system. You will need to send these steps to the CB.
You will need to figure out the ice pack situation. Find a method to keep the samples cool until they get where they are going. Your testing company should be able to help you with this.
You will need to get the testing company a list of people they are to call if the samples arrive in poor condition, and you will need to develop a plan what you will do in that instance.
-Setanta
Thanked by 1 Member:
|
|
#8
Posted 07 December 2023 - 05:24 PM
Probably purchase a small freezer to store ice packs in, then this won't be an issue
(our lab ships us coolers and ice packs to send back to them)
If October was missed due to NO available trained staff (assuming since you said you're new) then other folks need to be trained (as part of the corrective action) so this never happens again
AND this is part of management commitment---so maybe retrain them as well of the importance of tasks being done as per written procedures
Please stop referring to me as Sir/sirs
Thanked by 1 Member:
|
|
#9
Posted 07 December 2023 - 06:45 PM
If you're new to the industry, welcome! If you're only new to this company, man, what a rough spot to be in.
Ideally, before your audit occurred, you would have noticed the swabs weren't done for those months and issued a CAPA ahead of your audit. By owning mistakes like this ahead of the auditor finding it, you can often show them you remedied the issue prior to auditing and avoid taking a mark (if your corrective action has been monitored and no repeats of the problem occurred). It's not 100% going to get you out of a finding, but I've talked my way out of a few by noting we found and solved the problem first.
Now that it's into your audit report, you'll need to write a CAPA. You've already identified one set was out of spec, another wasn't taken at all. You'll need to develop a plan that avoids these errors from happening in the future, update your program, and retrain employees to follow the updates. Maybe a schedule where samples are taken early in the month with enough time to send a secondary set if they arrive warm/otherwise out of spec. For the ones not taken due to employee absence, designate alternates in your program who pick up the job in the absence of an employee (and make sure alternates have documented training).
Your program update will need to include some review now as well. You'll need to be able to prove you're verifying these tests are being done. Your program should also detail what you do when you discover samples weren't taken or samples were received out of spec at the lab. If there's time to resample in the same month, you should. If you find another set was missed in the future, your program should require you to issue a CAPA internally and figure out what happened again.
Thanked by 1 Member:
|
|
1 user(s) are reading this topic
0 members, 1 guests, 0 anonymous users